China Steel moves towards smart manufacturing: from bright fires to black lamp factories
The Black Light Factory, also known as the Smart Factory, got its name because the machines in the workshop can be operated automatically without lighting. Under the general situation of capacity reduction, in recent years, China’s steel industry, one of the pillar industries of China’s traditional manufacturing industry, has actively embraced the wave of intelligence.
In the past, people’s impression of the steel industry was “stupid and black”; now, relying on advanced technology, the major steel companies have long got rid of the past production methods and realized the gorgeous transformation of informationization, automation, unmanned and intelligent, Show a new production form.
What does an intelligent steel factory look like? What high-end technologies are used in the production process? The intelligent system of Baotou Iron and Steel (Group) Co., Ltd., one of the earliest iron and steel industrial bases in China, can be glimpsed.
Automatic production: industrial robots show their talents, labeling and packaging in one go
The dross hopper is immersed in the pond, and the dross in the pond is taken to the zinc trough… into the workshop of the Baotou Steel Sheet Factory, the “workers” are busy working on the production line. However, these workers are not ordinary workers, but intelligent robots.
Embedding robots into production lines and replacing humans to complete high-intensity, repetitive and even hazardous work is an important step for the domestic steel industry to move towards intelligent manufacturing. These automated equipment not only reduces the labor intensity of workers, but also improves the accuracy of work and saves many costs.
Wang Yong, deputy minister of the galvanized silicon steel department of the sheet metal plant, told reporters that after using the slag fishing robot in the plant, the slag production rate has been reduced from the original 10% to 9%. This reduction of one percentage point can be saved in one year. 600 thousand yuan.
At present, Baotou has already deployed industrial robots on multiple production lines. In the Coal and Coking Chemical Branch, the ammonium sulfate automatic packaging production line in the recycling area operates efficiently. The entire production line is composed of a palletizing robot system, a robot bag gripper, an automatic bagging machine, etc. The entire process from packaging to transportation is done in one go, clean and neat.
In the metal manufacturing company, the automatic labeling robot can not only label and scan the steel coil, but also verify the information of the steel coil and release it after confirming that it is correct.
Zhao Jian, a senior technical director in charge of intelligent manufacturing at the metal manufacturing company, told reporters that the company used to manually label steel coils, with an error rate of about five thousandths. After the robot is embedded in the production line, each robot can replace one shift (about 24 people) of workers, which can increase the labeling efficiency by about 10%, and the process quality is significantly improved.
In the steelmaking plant, the continuous slag adding system of the continuous casting machine and the “one-click” steelmaking mode allow the factory employees to say goodbye to dirty and tired. Zhang Meng, a steelworker, said with emotion: “In the past, it was necessary to manually shovel the protective slag from the bale to realize the slag adding operation. Everyone has to endure the high temperature smoke in the summer, and in the winter it has to endure the biting outside. Cold wind, now that the dirty work is done by robots, we only need to operate the computer.”
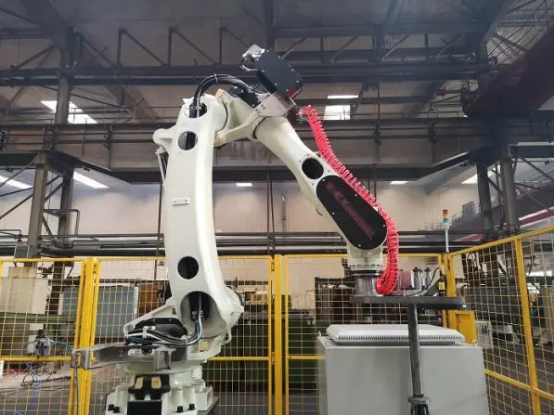
The picture shows the pipe processing coupling handling robot in operation at Baotou Steel Pipe Company
Guo Wei, Director of the Equipment Engineering Department of Baotou Steel Co., Ltd., said: “In 2019, we will establish 19 robot projects, and this year we have successively deployed 8 types of industrial robots such as end-face grinding robots and sampling and handling robots. While introducing equipment, we are also To strengthen independent research and development, several robots to be developed have been planned.”
Smart mine: full coverage of 5G networks
Baiyun Ebo, the largest iron-fluoride-rare earth comprehensive deposit in China.
In the Baiyun Ebo mining area of Baosteel, several 6.8-meter-high, 170-ton “large-block” mine cars can be seen along the established route to transport ore to the designated location without errors. You think that those who drive mine cars must be experienced “old drivers”, but in reality, these mine cars that are flexible in turning, encounter obstacles and brake in time are unmanned vehicles.
In the bright cab of the minecart, the steering wheel that was supposed to be controlled by the driver is now replaced by an electronically controlled steering wheel. Throttle and brake are all electric sensors.
Relying on advanced GPS and visual perception technology, unmanned mining vehicles can accurately perceive the surrounding environment; and the powerful 5G edge computing power and core cloud computing capabilities give the mining vehicles a “brain” for automatic hierarchical decision-making. Yang Nan, a staff member of the mining area, introduced that these high-tech mine cars can not only follow the programmed route, but also are not affected by the harsh environment, which can be said to be unstoppable.
As the first open-pit mine operated by unmanned transportation in the country, Baosteel Baiyun Ebo Mining District ushered in the first field test of unmanned mining vehicles in August 2018. Now, in less than two years, 4 unmanned mining vehicles have been officially put on duty in the mining area.
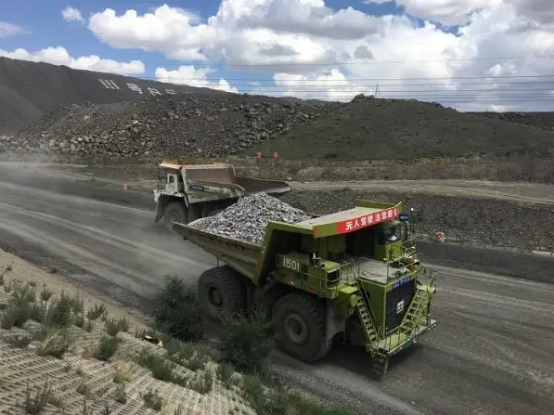
The picture shows the unmanned mine car in Baiyun Ebo iron mine is carrying iron ore transportation
According to Yang Nan, with the increase in the number of mining vehicles, the mining area relies on 5G networks to build a remote intelligent dispatch monitoring platform and a “vehicle-vehicle-vehicle-vehicle” communication system to realize remote control of vehicles and automatic obstacle avoidance. , Real-time scheduling. At the same time, the “open-air iron ore stone side-iron ore rough stone transportation mine card unmanned operation cluster” was built to allow the mine trucks to work collaboratively and cooperate with each other to minimize the number of on-site operators.
Automated unmanned mining vehicles are only part of the Baiyun Ebo Smart Mine Project.
Li Degang, deputy general manager of Baotou Steel (Group) Company and chairman of Baotou Steel Co., Ltd., said that the construction of smart mines is a complex system project, which currently includes three major parts. “The first part is self-driving. In addition to the minecart, we also have many forklifts that are also remotely controlled.
Baotou is very cold in winter, and the outside temperature can sometimes reach minus 30 degrees Celsius. Unmanned and remote control technology can reduce the staff’s burden.”
The second part is UAV mapping. “Drones can map the geography of mines and pass the data back. By analyzing the data, we can solve the problem of where and how much to pick every day. We can also rely on the data to build a digital model to optimize the mining process. Management.”
The third part is the dispatch system, which is the core of the smart mine. “Based on the data transmitted by the above two systems, we can monitor the entire production process and optimize the entire scheduling system to find the best control method. Currently, the ongoing construction projects include production intelligent scheduling system and intelligent mining area safety monitoring. System, intelligent management and control system of electric shovel, intelligent management and control system of roller cone rig, etc.” Li Degang said.
The reporter learned that for the entire mining system, an important keyword is “data”. The data transmission volume of the smart mine in operation is very large, and it must be achieved by relying on the 5G communication network. At the same time, because the 5G transmission speed is very fast, the network delay is less than 20 milliseconds, which can make the control of the mine faster and more timely.
“Under intelligent management, the comprehensive benefits of the mining area have increased by more than 10%, the overall energy consumption has dropped by more than 5%, and the level of energy conservation and environmental protection has also been significantly improved.” Yang Nan said, “With the rapid development of 5G technology in our country and the industrial Internet Construction, the future Baiyun Ebo mine will be a mine that integrates safety, green, wisdom, humanities and science.”
Intelligent warehouse: all data is uploaded in real time, and the entire process is automatically tracked
For a smart factory, it is not enough to promote intelligence at a single process point, but also to achieve the higher goals of intelligent manufacturing systemization, centralized control and one-click.
The unmanned intelligent warehouse is an important manifestation of Baosteel from the intelligent process to the regional intelligence.
In the cold-rolled intelligent warehouse of the metal manufacturing company, in the 100-meter workshop, only the mechanical equipment is working in an orderly and responsible manner. The robot affixes the label to the steel coil and applies a two-dimensional code to the steel coil. These two-dimensional codes are the “identity cards” of the steel coil and are the key information for connecting the Internet of Things in the storage area. Just scan it , The relevant data will be uploaded to the warehouse management system in real time, and managers can easily query and track.
The steel coil with the “identity card” stopped on the conveyor belt for a while, and then it was taken into the warehouse by an unmanned crane with two huge booms. Dong Bingwei, a technician at the metal manufacturing company, told reporters that these unmanned cranes suspended in the air are “flexible in terms of hands and feet” and can accurately identify and lift steel coils without any loss to the steel coils. At the same time, their safety performance is very high. The boundary of the crane is equipped with a yellow safety barrier. There is a safety door at every distance from the barrier. Workers must press the red button on the door if they want to enter the warehouse area. The door will be opened only after obtaining the permission of the management system, ensuring the safe and orderly operation of the unmanned library.
In the operation room of the storage area, the computer screen in front of the manager is displaying the three-dimensional modeling of the storage area, which is exactly the same as the actual operation of the storage area outside the entire model. Chief engineer Shi Aiwen, who is responsible for the design and transformation of the entire “intelligent warehouse”, introduced that the reason why the warehouse area can realize automatic tracking and control of the entire process is that it has a smart “brain”-the warehouse area management system, which has a huge information network , Through the intelligent driving scheduling, path planning, pallet allocation and other functions, the completion of the off-line storage of all steel coils on the five production lines, the on-line out of the warehouse, the stacking in the warehouse, and the unmanned operation of all driving and ground equipment can also be Real-time tracking of materials.
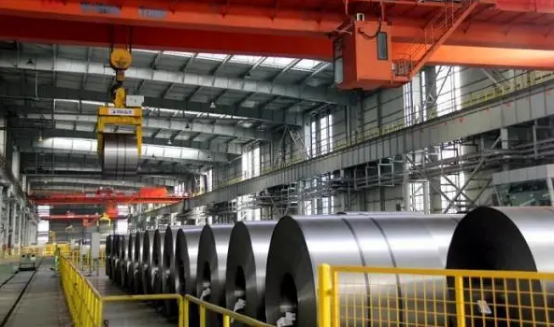
The picture shows the cold-rolled “intelligent warehouse” of Baosteel Metal Manufacturing Company
How is the intelligent warehouse better than traditional warehouses? Wang Jing, the person in charge of the storage area, said: “In the past, our storage system was manually located, lifted, and rewinded, which was prone to leaks and safety production accidents. For example, improper lifting by the driver will affect the quality of the product and the materials are in the process of circulation. Unnecessary wear and tear may occur. Today, the production in the warehouse is intelligent, not only the operation time is shortened, but also the steel coil hoisting rate is reduced by 90%, and the operation accuracy rate is greatly improved. More importantly, unmanned intelligence After the operation of the library, 36 crane drivers and 4 ground personnel were reduced.
At present, only 2 people in a class are responsible for the care and emergency operation of the crane production system, which can save labor costs 4.79 million yuan per year.”
Relevant reports show that many domestic steel companies, including Baotou Steel and Baosteel, have achieved unmanned operation in the reservoir area, and some positions that previously required the operation of lights have been equipped to turn off the lights. From declining to unmanned, from “physical work” to “brain work”, from process intelligence to regional intelligence, the traditional steel industry is stepping towards the “black lamp factory” step by step.